Tipton and Ratchet Clamps
General Manufacturing Line-Up Clamps
General Manufacturing Company is the pipeline insdustry's only source of external pipeline shipment clamps which offers an optional selection in cross-member bar design. With these options, the conctractor can order the clamp which will best do the job.
General clamps come standard with flat cross bars or with no-tack arched cross bars, in both hand-lever and hydraulic closure varieties.
KC. Ratchet Clamps
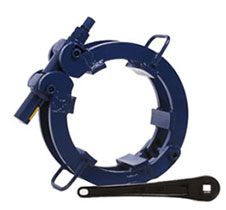
KC. Ratchet Drive Outside Line-up Clamps have been the quality leader of the pipeline industry for many years. This line of KC clamps are of the screw type and are operated with a reversible ratchet wrench supplied with each clamp. Along with conventional design, these clamps have two features that make them superior to other clamps. First, the inside diameter of the clamp is machined to fit the OD of the pipe being aligned. This machining operation produces a true bore with parallel pad faces, thus allowing each pad to fully contact the pipe surfaces to aid in accurate alignment of the joint. Secondly, KC. clamps are extremely rigid, being constructed of heavy rectangular bar stock rolled the "hard" way; a design which produces maximum rigidity for the weight of the stock being used. This rigidity enables the clamp to resist springing and distortion when clamping out-of-round pipe. These two qualities of accurate bore and
high rigidity combine to produce the best possible joint alignment.
The heart of the KC. Ratchet Drive Clamp, the screw, is made of alloy steel and is of sufficient diameter to withstand the stresses imposed by rigorous service. The screw threads are of acme configuration precision cut for maximum strength and long periods of smooth operation. Clamp screws are protected from dirt contamination by heavy telescoping tubular guards, and grease zerks are provided in the steel nut assemblies to allow lubrication of the screw threads and bearing.
Clamp pads are made of rectangular steel that is laid flat to maximize pipe contact and minimize the distance between pressure areas. After the pads are welded in place on the rings, they are bored to proper size and contour to accurately fit the pipe to be clamped. This feature, in combination with the clamp's extreme rigidity and strong alloy screw, results in greater clamping pressure. This pressure is evenly applied to the pipe insuring proper alignment before welding.